Degassing Valve Testing for Coffee Packaging
The client
We were approached by a major manufacturer of coffee packaging. Their factory produced hundreds of millions of coffee packages - these packages typically used a degassing valve inside each of the packages.
Coffee generates carbon dioxide inside the package. Typically the fresher & higher the quality coffee, the less it is roasted (relative to poorer quantity coffee). The less it is roasted, the more CO2 it will generate. If the very best coffee is not packed with a degassing valve, then the pack will inflate. An inflated package does NOT look good on the retail shelf and if often perceived ashaving ‘gone off’. Furthermore, if it inflates on the retail shelf it will not hold its vertical “placedposition”. At best the pack is likely to fall on its side, and at worst, will fall off the shelf onto the
supermarket floor. This is highly undesirable, will reduce sales and cause product losses.
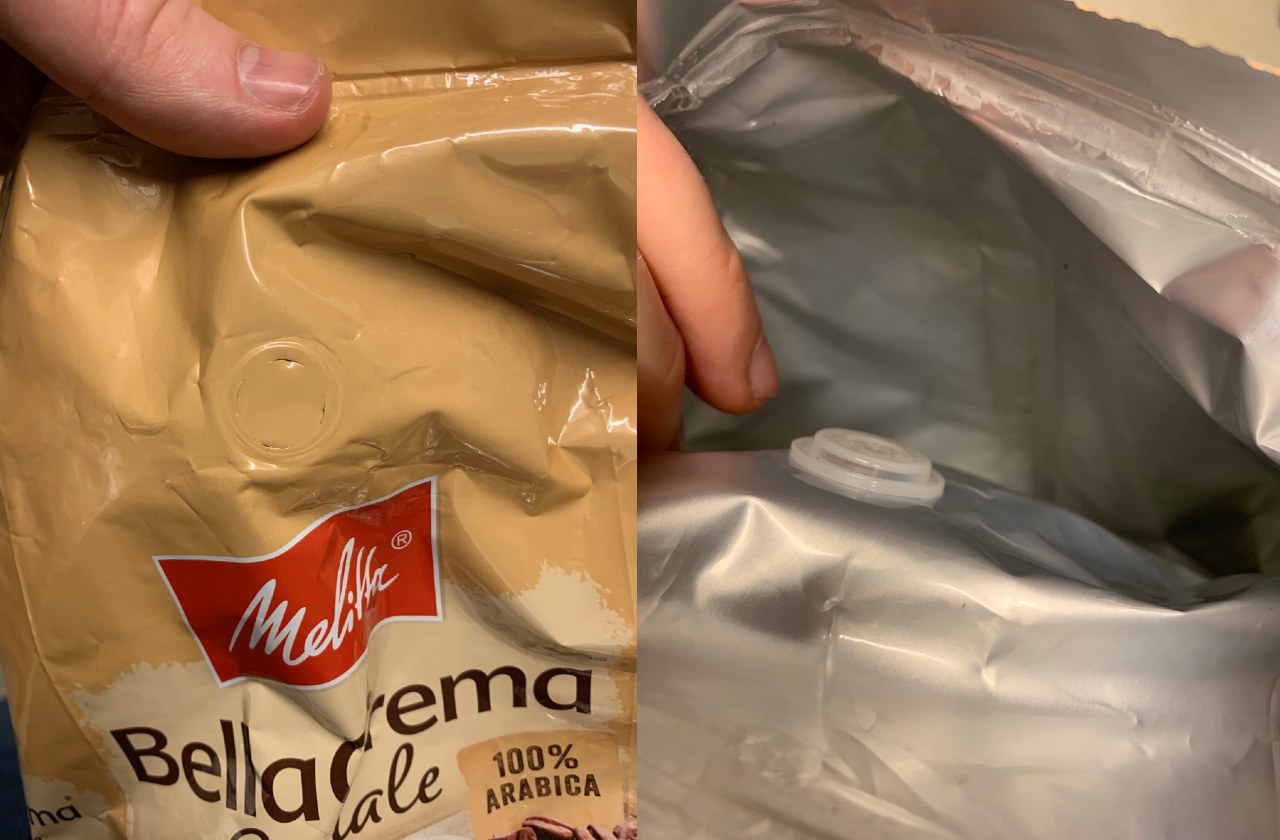
The Project
The degassing valves are heat sealed into the metallised laminate films and fabricated into coffee bags and pouches. Our client wished to provide the very best packaging for the very best quality coffee and they wished to have exceptional quality control protocols for their packaging. The
following conditions needed to be tested:
1) That the degassing valves are securely sealed into the packaging film.
2) That the Degassing valves would open (and relieve the CO2 over pressure) at the desired pressure.
We needed an instrument that would simultaneously measure pressure and flow and be able to measure when the flow rate increased relative to an increase in pressure. The solution need to be able to test the degassing valves independently as well as test the finished sealed packages with integrated degassing valves.
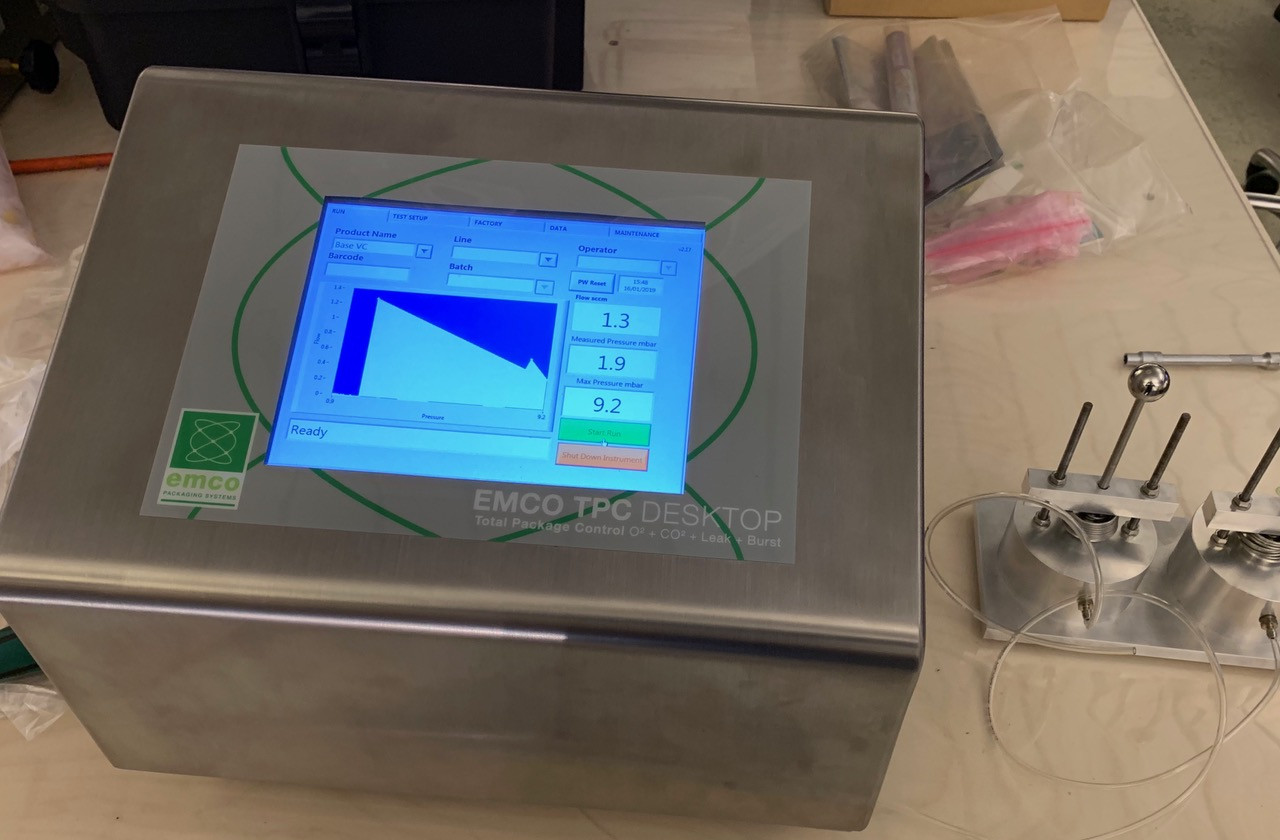
Solutions
We prototyped various flow and pressure technologies, electronic and manual. Additionally we prototyped custom manifolds to suit the different types of degassing valves that our client used. The TPC DGV (DeGassing Valve) Tester was born. This instrument was engineered to work with a needle and air tight septum, to test the finished packs and with a manifold to test the valves separately.
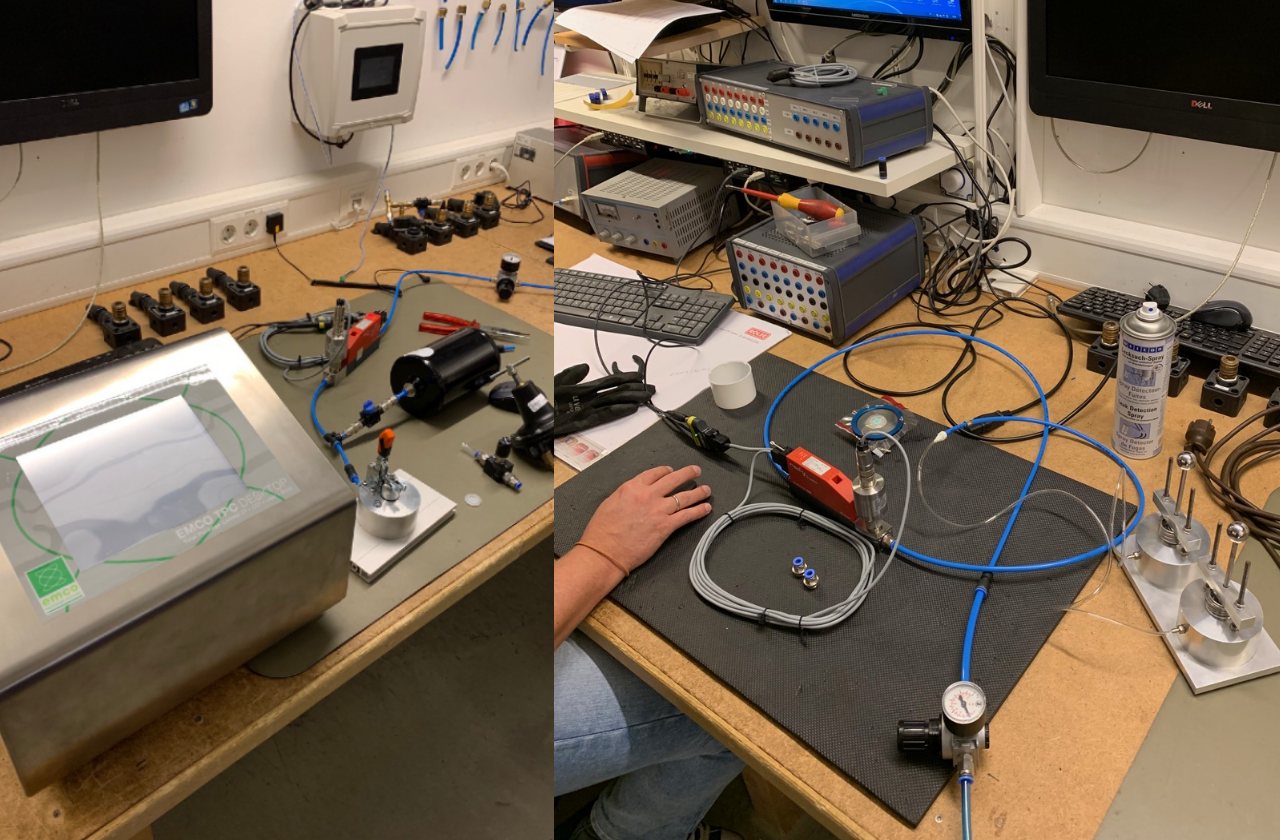
Results
The instrument has been a huge success. It has proven reliable and accurate (we can test andcalibrate the instrument with laser fixed leaks 5-500micron as well as with calibrated pressure and flow testing devices) and has provided a highly effective, fast & repeatable test protocol. This is empirically demonstrable to their customers and has resulted in new accounts and far less product rejections.